This thread is is to discuss the eLofty/Lofty direct drives. This includes the features, latest news, your reviews, upgrades, issues, failures etc. To avoid derailing the thread please back your opinion, both good and bad, with data. I’ll try to keep this first post updated with all pertinent information. Please let me know if you would like to have something useful added up here.
It all started with @BillGordon’s review of the direct drives. Followed by positive comments from @esk8jpn, @topcloud, @mishrasubhransu(me). Later @topcloud and @Winfly negotiated group buy prices for the drives and the relevant thread is here.
As far as I know these are the people who bought the drives: @esk8jpn, @BillGordon , @DAddYE, @hiboute(other forum), @Goldrabe, @Njull69(other forum), @landonkun, @river and @ryansinatra; and maybe able to help you with additional questions that I may have. Please let me know privately if you rather not have your names tagged here.
You can find the rest of the information from the builders forum here.
Specification
Number of Magnets/Poles: 20(this is what you use in VESC)
Number of stator poles: 18
KV: 58KV(even though it is advertised at 75KV(however @Goldrabe seems to have gotten 75KV motor ))
Vesc Detection:
To get the KV of your motor use the following formula:
KV = 26672erpm / (10pole_pair*38.5Volts*0.95duty_cycle) = 72.92.
Where you get the erpm, battery_in_voltage, duty_cycle from the vesc_tool realtime info by taking a screenshot while at max throttle( then duty cycle would be 95% i.e. 0.95).
Known Issues
Issue: Braking is very soft at low speeds. This is an issue shared by other direct drives/hub motors too.
Solution: Use current mode with a low reverse speed limit(I chose 4km/hr ). This uses active braking as opposed to locking the brakes at very low speed. With this I can come to a stop even on a decline slope. I used the vesc_tool mobile app to set the speed under the profiles tab. If you use metr pro, it can be done through modes.
Issue: Motor getting hot when climbing hills. If you look at the motor detection results, you can see that the internal resistance(IR) is 85mOhm. My flipsky 6374 motors have IR of 13mOhm. Heat produced is i2R so that tells us that the heat produced by 50Amp in 13mOhm motor will be same as 20Amps in 87mOhm motor. I wonder what other direct drives compare here.
Solution: Use lower limits on current than what you would use on geared drives. VESC automatic current settings are good, but you can push them a bit more(5-10Amps more, but be careful). To truly solve it, the IR should be reduced(open ended problem). I use +50/-60 for motor current in VESC and very happy with it.
How to buy
The best way is to talk to Kenna( with username kenna on the other forum, but rarely active) over email or whatsapp( + eight6 13four 1186 842three).
Price
Following was group-buy price so please use that in reference when asking for single qty price with Kenna.
Sensor wires
The white temperature wire may or may not present in your model
Pics
TKP setup
I paid a total of $22 for all the things needed for TKP setup.
1 X pack of pivot cups, bushing and nuts
2 X base_plate
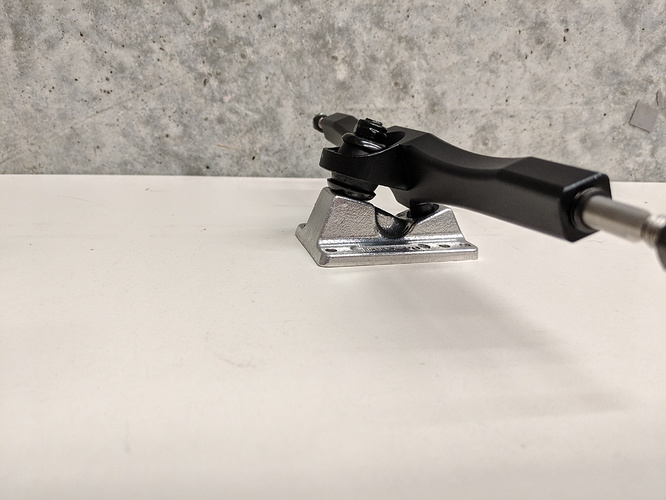
Pneumatic setup
3D printed hubs:
Files are here.
After falling 3 times, in a month, because of stupid rocks, street plates bad roads, I refuse to ride thane anymore. I have already nearly 900km on 6" pneumatics and haven’t had a single problem since. So the only way I would these DD would be with pneumatics. Due to lack of available versions I made 3D printed hubs that directly works with these drives. I printed them in PETG . It’s been working great so far(50kms or so). Ideal material would be nylon, if you can access it. “Taulman Alloy 910” would be my recommendation.
Print Settings:
Material: Nylon(Recommended), PETG or ABS. PLA+ might also work.
Layer Cooling: off(To increase layer adhesion)
Infill: 100% and concentric(prints like walls)
Walls: 6 Walls
3D printed hub adapter:
Currently only the Bergmeister 150mm wheels are supported. It was designed by @landonkun and tested by @DAddYE . The files are here:
Aluminum hubs:
CNCed
@Janux-esk8 or @marcmt88(other forum), manufactured a sample for @topcloud and might be able to do it for you too. Edit: they are now available at janux-esk8.com
(Following 2 images are from @topcloud’s post on other forum)
Casted and CNCed
I modified the 3D printed parts to be more suitable for production using casting and followed by CNC. This is still in development. I made a poll here to guage the interest in such a hub here.
These wheels can also be used with a pulley, if you have a change of heart.