i think when they say the inertia filters out the effects…by “effects” i think they must mean at higher speed the cogging torque waveform is imperceptible as the cogging torque waveform is still their overlaid on the output torque at all speeds but at higher speed the inertia makes it imperceptible in typical use. judging by how all of us will feel the board slow down when coasting that aspect of the cogging torque is not being filtered out. when the coils and teeth are electrified i dont think they would experience cogging and their electrically formed polarity will replace as apposed to being overlain on the cogging torque.but i might be forgetting and have seen it described as overlaid on the output torque as well
when they say techniques used against cogging torque i think theyre meaning solely in the motor design and the common techniques of skewing something will reduce running torque. software takes current to overcome the cogging torque. but the mellow motor maybe is an example of overcoming cogging torque with maybe no loss in running torque and in simulations ive done just shrinking the gap between teeth it didnt show a reduction in running torque (seen by just seeing if the kv goes up).
i think often when talking of cogging torque it is only talking of the waveform and how it gives a loss of position precision and they arent talking of the loss of momentum. that loss of momentum…and if its actually eddies or hysteresis is what im trying to find. ive not seen any examples of a low cogging motor having less iron losses, which would make sense if it were to to iron losses, but do often see the opposite. theres other variables for sure but generally that’s how it seems to go
1 Like
Skewing the slots eliminates the cogging torque but not the iron loss. Iron loss slows the rotor. Without the iron loss, cogging torque can’t change the average speed of the rotor, since the effect both stores and then releases magnetic potential energy (net 0). It’s just like without friction with an initial push you can maintain average speed on a rolling set of hills, as long as you have enough momentum to crest the hills, because in that case you’re storing and releasing gravitational potential energy. So a similarly constructed skewed motor would still resist coasting but without cogging.
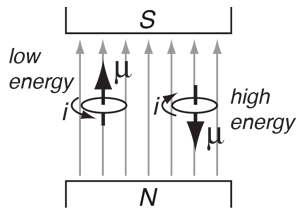
1 Like
electric bike hub motors sometimes will use a skewed stator so as to have a better coast. cogging and the lack of coast seem to go hand in hand, and the skewed motor is likely to have more iron losses. the mellow hub motor seems the best example of a motor with low cogging, a good coast, and no detriment to output torque.
With sufficient rotor momentum to overcome the cogging “crests,” you’d have to show how and where the rotor’s energy transfers via “cogging torque,” without invoking eddy currents or hysteresis, both of which fall under “iron loss.”
1 Like
there’s the possibility a cogging motor ruining a good coast could have no losses since a magnet can be a source of pretty much endless energy depending on it’s orientation. its not free energy in that it needs to be oriented correctly but the spinning motor would be a means of badly orienting the magnet. This would be just like when the motor is producing productive power when electrified and the magnets through their orientation are adding to the work being done. if it’s not eddies or hysteresis, which it may be but so far I havent seen evidence of that and have seen evidence of just the opposite, it seems the only option and not far fetched.
1 Like
Looks like Trampa liked this one.