+1 for team BMS…makes life simple, try picking up one of the fancy new smart BMSs and you’ll be happy about it
Seems like more onboard electronics is probably not the solution.
I do like @magharees idea of a waterproof aviation connector. I’ll probably switch to that.
But I also have to beef up the seals around the battery box as well, and I’ll still add a lot of fuses
A smart bms will give you a real time display of what’s going on with your battery, it’ll also eliminate that changing nightmare that probably caused your fire to begin with. Either way, glad you didn’t lose more in the fire.
Can you send me a link to these smart BMSs?
Thanks,
Ah man,
this is not how i imagined this thread going.
sad for you and the board, at least nothing further got damaged. Salt water is an absolute bitch.
probably was a drop of water drying and forming a salt crystal bridge across contacts that did for it.
really hope you revive this in the future, the beach is a fantastic playground.
Get in on this
I bought a fire extinguisher today, why I don’t know cause we have one already, so I’m blaming you Doug
Loved this thread I’m happy no one was injured in the fire
Thanks all. I’m having a difficult time getting back to this project. Somewhere it seems like there’s a rule that says if a project bursts into flames that’s kind of it for the project.
I actually had a job once where one of my circuit boards caught fire. It was based on the design of my predecessor so wasn’t really my design, but I was the Tech. It was pretty clear that I wasn’t going to be keeping that job (which was for the better really) after that.
So at the very least I’ll probably just let this thing sit until next spring.
I am not sure what to do about the surviving cells. I have 3 packs (30 cells) that are slightly stinky but perfectly good. BUT if they took any damage because of the salt water or the fire I would never trust them. I have no way of knowing. So I guess I’ll just let them sit until next spring as well. I’ll probably run a bunch of full charge/discharge cycles in fire-proof isolation on them before I put them back in the board. Seems like the greatest chance of a fire is at the end of a full charge cycle. I mean, you know, other than shorting them
Anyway, that’s where it sits.
You got any other projects in the works? Your engineering is honestly inspiring
I do actually, I’m going to get back to my eFoil build.
because, you know, I haven’t had enough trouble with batteries and water
Well at very least if you’re efoil start burning when you’re ridding it, the you won’t die dicaprio’s way
That’s frightening !!
If it happened to someone (like me) less experienced about such situations than you, it will ends up in total disaster.
I’m considering building a safe battery storage…
I miss this kind of threads !
@DougM any new project running ?
This year is full of new cool buyable stuff for us, but i see less and less very innovative/hardcordDIY stuff lately
I’m back!
Spring is right around the corner and it’s time to start thinking about rebuilding this board.
I recovered a little over half the cells from the fire, and although they are slightly discolored they don’t show any real heat damage, so I’m comfortable re-using them. For the rest, which spent the winter encased in concrete in my back yard, even though I think only 1 cel actually flamed out, I’m going to kill and recycle the rest.
So 3 changes need to be made.
- I need to go to sensored motors. Push starting on pavement, and even MTB is pretty easy, and I prefer it anyway to get stable before applying power, but in sand it’s a disaster. There’s so much drag that you literally have to dance between applying power and getting the board moving in the sand without you on it, then jumping on and gunning it, but not too much power. It turned out to be a real pain in the ass.
Also, more power. I ordered some 6380 sensored, battle hardened motors that were recommended by a friend. I know what you’re asking, “but Doug, don’t you hate flipsky?” Well, yes, all their electronics failed me and I threw the whole of them away, but apparently their motors are ok because this particular friend is the most hardcore eMTBer I know and if they survive his abuse they’ll be fine in the sand.
- new battery pack. I’m making some mechanical changes in the way the battery banks mount into the frame (they’ll mount from the top rather than the bottom as the bottom will now be sealed). But basically everything remains the same except obvously there will be fuses integrated into the balance leads for every bank.
And obviously the charge ports will be the waterproof aircraft kind
- seal the battery box. This is actually a lot simpler than I thought it would be once I decided to install the battery banks from the top that allowed me to make the bottom more or less permanent. I’ll still use the orange plastic as the cover, but I will be using VHB tape to permanently seal the cover to the end caps. The sides of the cover will still be screwed into the extruded rail, but there will be closed cell foam to water seal, and a thick(ish) plastic strip to make sure that the cover is secure to the rail.
Pictures and, since I’m trying to become a Youtube sensation, videos coming.
Hes back everyone, hes back!
You made my day man
So I started by re-printing and cutting all the parts that burned, melted and otherwise smelled funny after the fire. This was basically everything plastic that was in the battery box. Most of them were 3D printed, a few of them were 2.5D CNC carved.
Here’s some of the new 3D printed parts (in PETG this time but otherwise the same part):
and the new battery cage ends:
Note that the way these mount to the frame has changed completely. Where the old ones bolted to the bottom of the extruded rail these slide inside the rail and have a mount clip that holds them in place. This way I can close up some unfortunately large water entry points.
The new circuit boards:
which have fuses on them (see, I can learn from my mistakes)
And here’s the new charge ports:
I went seriously overboard on making sure that no salty water came into contact with, well, contacts.
Now, on to more thorough waterproofing. I started with Bud fittings (Gland fittings if you are Googling or Amazoning). These are basically IP65 rated wire seals. Here’s a bunch of them in a cardboard box
and while this isn’t a great angle for showing how they work here’s a shot of them attached to a battery box end cap.
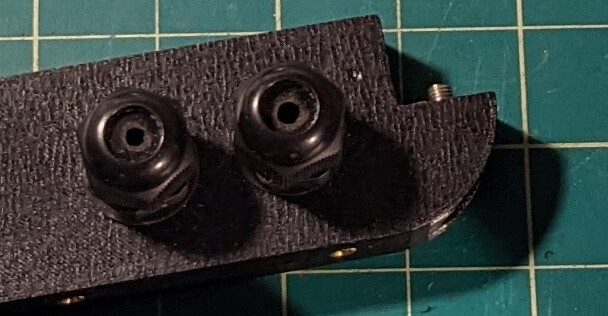
Oh, wait! here’s a nice shot of them in dress rehearsal:
(don’t ask about the blue tape. That was a really bad day. I’ll fix that eventually)
I’ll talk a little bit more about how I’m going to seal the bottom of the box in a later post because I haven’t completely figured it out yet.
Here’s a sexy shot of the parts being 3D printed on my bling print bed:
I had to crack the transmissions because there were a few shortcuts I took in the original build that left un-checked would have allowed water in. And I have these shiny new 6380 sensored motors that I wanted to replace the old un-sensored motors with.
While I was in there the I noticed a couple of problems.
The first is rust. A lot of my screws weren’t stainless steel and really took exception to being soaked in salt water. So I’ve got a lot of stainless steel screws on order.
the second is that one of the drive gears was rubbing on the plate underneath it, causing a lot of scarring and eventually probably would have locked up or at least made a lot of noise.
The third is that the driven gear was a little too wide and rubbing against the bottom of the drive gear and might have been causing the driven gear to not quite settle into the housing straight. Might have been at a bit of an angle. Based on the scarring it wasn’t too bad, but I machined out the black stuff so it has some clearance now.
Last the way that the original motor was mounted to the transmission had the unfortunate consequence of the wires from the motor coming out directly over a screw in the transmission housing that I wanted to use to mount the motor covers. So I had to re-design and re-CNC the inner aluminum plate to move the mount holes around. I don’t have any good pictures of this.
That’s this week’s update. Stay tuned for next week when I make way too many words about closed cell foam.
So only the most attentive of you will remember that right in the middle of the original build I decided to redesign the gearbox housing, but I only updated one of the gearboxes to the new housing because the other one was already complete and no sense in rebuilding it for no good reason.
Well. Now I had to rebuild it, as well as retrofit the other housing, because the mount holes for the motor covers had to move.
This is where things get weird. The outer cover didn’t change at all from the first build, but when I went to cut a new one my holes went a wandering:
The holes are the first machine op in the script, the outline is the second, so the fact that the outline cut perfectly means the machine didn’t lose track of anything, these two holes are obviously the result of bit rot.
So I re-built the job in CamBam and re-cut the part et voila! Perfection:
While that was cutting I worked on the battery tub. It has to be as waterproof as I can get it, but also the screw holes have to line up between the extrusion, the orange plastic, and the black plastic reinforcement strips. No small feat.
Lots of time was spent marking and making little fixtures to make sure all the holes aligned, but in the end it went together pretty well.
I noticed during the process of building this that the orange plastic does eventually form to the curvature I forced it into, so my plan is to leave it together for a couple of days, then go back, remove it, install the closed cell foam (told ya I was going to talk about it) between the orange plastic and the end caps to make the seal waterproof.
Another foam seal will go along the top of the end caps and the top of the extruded rails, and will seal to the wood deck. That should give me good solid IP65
Well, almost. The channels in the extruded rail are a clear and thus far unobstructed path in, so I’ll jamb those up with blobs of foam.
Next, as I said before, was replacing all the rusty screws with 316 Stainless:
Aaaaaaand we’re off to build some battery banks:
Stay tuned for next week (possibly tomorrow) when I whine about how short the leads are on the Flipsky motors. There are a number of changes I need to make to the electrical box but it’s up high on the back to keep it out of the water, and I’m concerned that in its current location it’s too far away from where the motor leads come out of the transmission.
So I know what you’re asking, but Doug, what happens when you don’t model every part of your assembly? Well, you put your holes in the wrong place, that’s what. In this case the holes for the Bud fittings on the bottom of the control box interfere with the extruded rail.
So I had to re-cut that piece.
Next challenge was that because a long long time ago I decreased the number of teeth in the drive gear to try to get more power the result was that the location of the motor moved too close to the truck mount
So I had to do a bit of singing and dancing to get the motor cover to not interfere with the spinney part. But they look kinda cool.
There is a pretty good chance that these are going to get broken somewhere along the line. They are Z on the height axis, which means one good smack and they’ll come apart. I will put together a new design that uses my not-patented strategy of putting a threaded almuminum rod through the whole of the Z axis so the whole things stands in compression (see my post about the control box)
But for now I’m going to let that go.
Next up was final assembly of the tub. I installed the closed-cell foam on each of the end caps
and reassembled the whole thing hopefully for the last time.
I did figure out what I’m going to do about the channels in the extrusion. One of my favorite glues, for many weird reasons, is E6000
because it holds really well but comes off clean.
I’m going to try to get it into a syringe and inject it into each of the channels to seal them up. I was going to use hot glue but once it cools it doesn’t stick very well and is likely to pop out.
Next up is completing the battery cages
And one funny story (you know, funny in a sad and frustrating way). There was a website that had a contest - design a custom housing for your Hoyt remote and if you won they would send you a free professionally 3D printed version of your housing in nylon and a complete set of Hoyt guts so you could build and use it.
I got super excited, and I actually, because I’m trying (and mostly failing) to become a Youtube sensation, recorded the entire design process, and went to enter aaaaaaaaaaand, the contest had ended a month prior.
But here’s the design - I went ahead and got a version printed and I’m going to use it on the maiden voyage of the new Sand Runner.
The thing I like about this design, and the thing I don’t like about the Hoyt, is that the circular version of the remote doesn’t give you very positive location feedback in your hand - so you have to carefully adjust how you hold it so the thumbwheel is always in the right place.
My version solves that problem, but creates another problem, which is that the remote is specific to left-handers. Or maybe right-handers. I’m left handed but I hold the remote in my right hand. I assume that right-handed people hold the remote in their left hands. Maybe they don’t.
Anyway here we are. If you look closely you can see little bumps in the remote. Those are because the Hoyt screws are too long and I didn’t realize that until they became unusually tight