This seems super ambitious for one’s first battery.
Your 8 parallel cells do not require thick conductors joining them, the 20 series connections do.
I see most high amp battery packs use doubled or tripled 12awg silicone wire or tinned copper braid as series connects.
I’ve also read that the cans of P42a are more difficult to spot weld.
I’ve only built one Esk8 battery so far.
I made plenty of mistakes
I learned tons in the process.
I’m glad I decided on a small pack of inexpensive cells to learn with, and I actually made two 3s1p batteries first, one with 0.15 nickel, the second with 0.15 copper/0.10 nickel plated steel sandwich, even though these packs will never see more than 4 amps, and only briefly.
I thought I had the copper nickle method down, and tried it on my 10s2p battery with infinite slot method, and then found welds which appeared, to the eye, to be wonderful, were indeed totally and cometely inadequate.
More practice with my welder maxed out, could not weld 0.15 copper nickle sandwich on my new cells, but seemed more than awesome, on my practice cells.
I had to step down to 0.1 copper and 0.1 nickel plated steel to get proper welds on the new cells, and this battery will never see 30+ amps and will only approach that for a second or three.
A single layer of 0.15x10mm would have been far easier, and more than adequate.
But yea, I wish it were 24s 12p battery with P50b cells, welded with 0.3mm copper feed, 2 awg series interconnects, 4 2000 watt motors, and smoke this guy in a drag race.
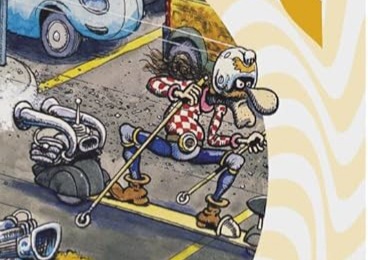
I get the desire for a huge battery with massive interconnects.
I remember searching for nickel and copper ampacity charts, and finding those one you linked, and look back at how much less I understood then, than I do now, having built only one (untested) battery so far, and how much more I still need to learn.
I am very glad I started with a modest size and capability Battery with 40$ worth of cells.
20s8p … 160 P42a cells at 4.60$ each…760$
I’d be dang sure of my skills before taking on such a battery, and one can only learn so much by reading, watching researching.
Experience teaches far better.