I’ll probably install Matlab later tonight so that you don’t have to bother generating all the graphs, but here is all the data from my motor tests. Also I first ran the 95% duty cycle test, and then the 35% one. Just because the 95% test normalizes all the values faster.
Edit: Matlab isn’t FOSS? Yeah, no thanks. You generate the pretty graphs please!
I’ll lookup all the manufacture given motor info in a bit and add it in for you… Edit: done.
All tests done on a Stormcore 100D and a fully charged 12s Li-ion pack. FW 5.3 2021-07-14
Maytech 6355 190kv
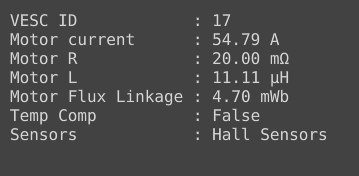
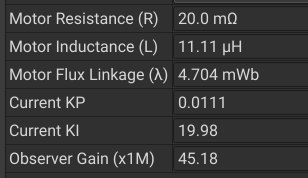
95% duty
0.37A
55009 ERPM
35% duty
0.35A (0.44A on first test, but I guess ignore this value)
20602 ERPM
14 poles = 7 pole pairs
Manufacturer rates at 55A, 65A max.
Comments: New. Unikboards branding.
Maytech 6355 170kv
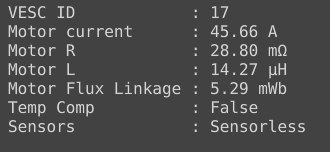
95% Duty
0.29A
48770 ERPM
35% Duty
0.32A
18208 ERPM
14 poles = 7 pole pairs
Manufacturer rates at 55A, 65A max.
Comments: slightly used
Maytech 6374 190kv
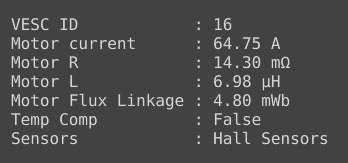
95% Duty
1.74A
53000 ERPM
35% Duty
1.05A
19790 ERPM
14 poles = 7 pole pairs
Manufacturer rates at 60A, 65A max.
Comments: new
Maytech 6880 180kv (same sized stator as 6374)
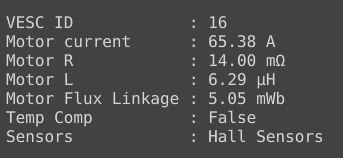
95% Duty cycle
2.25A
50000 ERPM
35% Duty cycle
1.30A
18740 ERPM
14 poles = 7 pole pairs
Manufacturer rates at 60A, 65A max.
Comments: New. Bioboards branding.
Maytech 6374 170kv
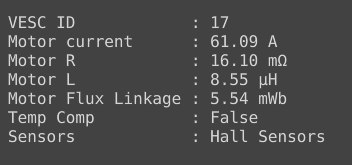
95% Duty cycle
0.92A
45860 ERPM
35% Duty cycle
0.65A
17150 ERPM
14 poles = 7 pole pairs
Manufacturer rates at 60A, 65A max.
Comments: New. Factory battle-hardened.
Maytech 6374 150kv
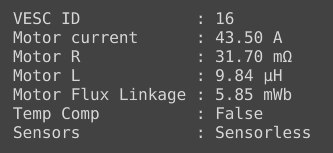
95% Duty cycle
0.95A
43250 ERPM
35% Duty cycle
0.85A
16125 ERPM
14 poles = 7 pole pairs
Comments: Been through hell and back. Somehow still runs great. No sensors tho. Unikboards branding.
Flipsky 6384 140kv
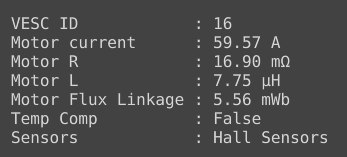
95% Duty cycle
0.88A
45470 ERPM
35% Duty cycle
0.80A
16969 ERPM
14 poles = 7 pole pairs
Manufacturer rates at 95A max.
Comments: New. Factory battle-hardened.
TorqueBoards 75kv direct drive
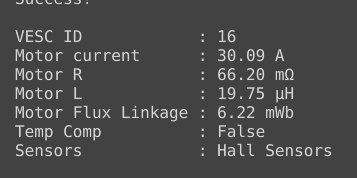
95% Duty cycle
2A
40560 ERPM
35% Duty cycle
1.65A
14840 ERPM
28 poles, 14 pole pairs.
Manufacturer rates at 80A.
Comments: Used.
Loaded x Unlimited 75kv hub motor
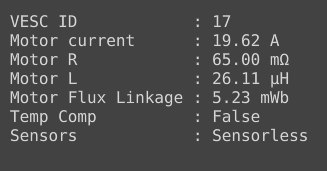
95% Duty cycle
1.15A
49130 ERPM
35% Duty cycle
1.05A
18060 ERPM
14 pole pairs = 28 poles, surprisingly enough
Source: this and speed calculations
Loaded unlimited hub motors experience? - #117 by glyphiks
Manufacturer rates at 20A.
Comments: New.
Can’t wait to dig into all this data and do comparisons 